Clover grass: Green refinery instead of imported soy
By Gustav Alvermann
Disrupted supply chains in a globalised economy are a highly topical issue. If certain raw materials are only available to a limited extent, the production process comes to a standstill. Agriculture is also familiar with such dependencies. In crop production, it is the imported energy for the production of synthetic nitrogen; in animal husbandry, it is the seemingly alternative-less soya. Even organic farming, which relies on legume nitrogen and its cycles in the system, has made itself dependent on organic soya imports for chicken and pork. These come from Eastern Europe and, interestingly, at least until recently from China.
Soya as high-quality protein source is becoming increasingly scarce
Because certain supplies do not come as usual, because transport has become more expensive, because organic laying hen farming has doubled in the past ten years. And last but not least, because the 5 % conventional ingredients in feed rations that have been permitted up to now will be largely eliminated by the EU requirement of 100 % organic feed from 2022. High-quality protein sources with a high methionine content will become very scarce, especially for laying hens. Until now, conventional sources from the starch industry, such as potato protein with a crude protein content of 76 % and maize gluten with 60 %, may be mixed into organic rations at 5 %.
A lack of sulphur-containing amino acids is critical for poultry
Home-grown beans, peas and lupins can largely fill this gap for pigs but not for poultry. They contain too little of the scarce sulphur-containing amino acids. Moreover, they are not really restorative elements in crop rotations. Drought in the crucial growth phase (flowering in June) has resulted in an organic average harvest of just 2 t/ha in Germany in 2021, for example. In perspective, these "quantities" flow into dairy cattle feeding and to a certain extent into pig feeding. The demanding chickens are not helped by this. Oilcakes from rape, sunflower and soya are more suitable for them. But their regional production is developing only slowly. All in all, high-quality protein sources are thus becoming of limiting importance for the organic poultry sector in the same way as microchips are for the car and tractor industry.
Concentrated amino acids
In this context, it is interesting to note that lucerne, clover and grass contain the coveted methionine/cysteine in a more concentrated form in terms of protein content than our domestic threshed legumes. Their protein is comparable in value to soy protein.
Clover grass grew better than ever in 2021. Its perennial growth catches phases of good water supply throughout the year; the roots of clover and lucerne also retrieve the limiting factor from deeper layers. 100 dt dry matter/ha can then be achieved in three to four cuts. With an average of 18 % protein, this means 18 dt of pure, high-quality protein per year. The big "but" should not be concealed: Unfortunately, the protein is packed in crude fibre, so that a monogastrician has only limited access to the coveted content.
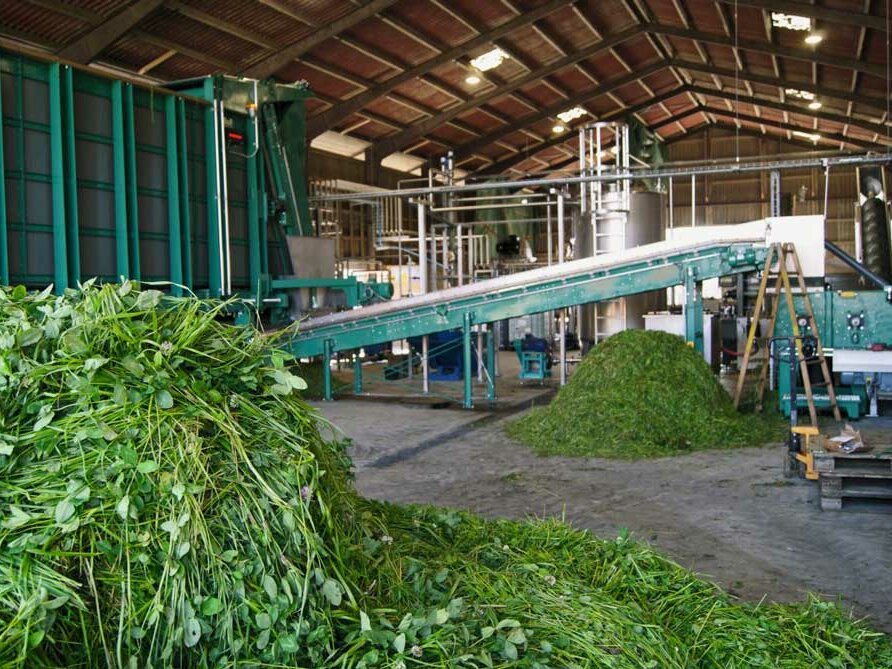
Photo: Petersen
The idea of a green refinery
This high-quality "green protein" must thus be extracted in order to use it for the nutrition of chicken and pigs - in the long term, possibly also for humans! The principle of this idea from Denmark is not entirely new. The term "refinery" creates the expectation that the process is complicated and expensive. In principle, however, it is quite simple. It is a two-step separation process. In the first step, the freshly harvested clover grass is sent through a screw press. You can imagine this as separating liquid manure. The result is a liquid phase, in which about half of the green protein is found, and a solid press residue.
In the second step, the protein-containing liquid is "thickened" by acid, similar to making cheese from milk. The "curd" is then centrifuged. The remaining whey, which the Danes call "brown water", is again part of the by-products.
It works on a laboratory level
Danish scientists have been working on this for several years. They could kill many birds with one stone: the protein from clover grass could replace soya imports 1:1, crop rotations would be supplemented by the forage cultivation with legumes that has been lost in the meantime, and a higher proportion of the nitrogen supply would be provided by the "solar energy" of the legumes. No wonder that Danish politicians are also very interested: a wonderful story for the transformation of modern society! Only - who will touch this in practice? Which agricultural entrepreneur is able to transfer it to the real economy at this stage of process development?
The Ausumgaard farm
There are now actually two of these green refineries in Denmark. One is located on the Ausum-gaard farm in northwestern Jutland. The initial conditions are favourable. 700 ha of arable land were converted to organic farming a few years ago, and a biogas plant is operated on the basis of clover grass and manure. However, the biogas process does not need the high protein content of the clover grass, as the aim is to generate energy. Thus, the upstream connection of a green refinery for the extraction and monetary utilisation of the protein sounds logical. However, this is a seasonal business. Only freshly cut clover is processed. The harvesting process is similar to the fresh feeding of clover or grass on farms by loader wagon - only slightly larger in size.
The plant was inaugurated at the end of the 2020 season
The practical experience is thus marked by the year 2021. The farm manager Kristian Lundgaard-Karlshoj now drew a positive conclusion: The technical process works. The protein content of the finished product is high. The project has great potential. The final stage of expansion is to process the growth of up to 800 ha of clover grass. In this way, the farm would involve regional organic farmers in the supply and also in the economic utilisation of the press residue - in the optimal case in dairy farming.
It is still difficult for the observer to imagine the dimension
Clover grass provides about 40 t/ha of fresh mass within five months without wilting. That is 0.25 t/ha per day and possibly 0.5 t/ha or up to 400 t per day during the main growth period for the planned total area of 800 ha of clover grass. This shows the dimension that is being considered here, whereby a large part is certainly diverted for silage preparation as winter fodder, especially in the main growth period, because both the cows and the biogas plant are year-round operations. Nevertheless, the small extrapolation shows that we are talking about processing 100 t of fresh mass per day or more. Ausumgaard says it has invested about €4 million - about half of which came from a public subsidy. One wonders: can this be profitable? According to the Danish consultant Christian Petersen - himself also an organic farmer and organic layer farmer and thus very interested in the outcome of the project - everyday life and successful continuous operation have not yet arrived. There is still tinkering and fiddling. Pushing clover grass through a screw press is not as easy as with other substrates. Moreover, the protein yield from the original substrate is "only" 45 %.
For the overall calculation, it is therefore not insignificant whether the press residue is used monetarily in cattle feeding or not. Only pressing the protein and then returning the residue to the field as fertiliser would probably be as economically interesting as a biogas plant without a heat concept.
Protential of clover grass protein: Christian Petersen sums up
"The economic level of imported organic soy has not yet been reached. However, improvements in the production process and favourable framework conditions lead us to expect this in the foreseeable future." With an optimistic assessment, the Danish consultant sees about ten such plants spread across Denmark in the next five to ten years. He counts an expected EU investment subsidy among the favourable framework conditions. Locally, the availability of organic farmland for the production of the substrate as well as cows and biogas plants for the economic utilisation of the by-products are decisive.
Conclusion
Producing high-quality protein for poultry from clover grass - the idea is fascinating and is already being implemented in Denmark. However, most organic eggs from green protein are still unlaid. In Germany, too, it will be up to resourceful and courageous entrepreneurs to bring about the everyday viability of a green refinery and the competitiveness of extracted clover protein vis-à-vis imported soya. The more favourable factors come together, the more likely this is to succeed.