Sensory Evaluation 4.0
Significance and Perspectives of Digitalisation in Sensory Quality Control and Product Development in the Food Industry
DLG Expert report 15/2018
Author:
Susanne Aegler
Food Engineer, graduated from Swiss Federal Institute of Technology (ETH)
Product Manager for Software SensoTASTE and Specialist for
Sensory Consumer Research / Sensory Education at SensoPLUS, Switzerland
susanne.aegler@sensoplus.ch
www.sensoplus.ch
Contact:
DLG e.V. (German Agricultural Society)
Competence Center Food (Fachzentrum Lebensmittel)
Bianca Schneider-Häder
Sensorik@DLG.org
Contents
- 1. Background, definition and goals of Industry 4.0
- 2. Digitalisation along the value chain: Focus on consumers and the food industry
- 3. Digitalised quality assurance in the corporate process
- 4. Importance of digitalisation for sensory evaluation in the food sector
- 5. Software offers for the digitalisation of sensory evaluation processes at a glance
- 6. Digitalisation throughout the product life cycle
- 7. Outlook
- 8. Selection of software programmes in connection with sensory evaluation
- Literature, references:
- kontakt
In the food industry, as in other industrial sectors, impulses are being set for the digital future. The human being is at the centre of the tasks to be mastered in the context of Industry 4.0 and is challenged to use the opportunities offered by information technology and digitalisation and to keep an eye on the possible risks. This development does not stop at the field of sensory evaluation. In many companies, data collection, evaluation and administration of human sensory tests are already computerised. In this respect, various software programs are offered on the market that support the processes around sensory quality assurance and product development. However, further networking and automation of data management of these areas within the company, as well as with suppliers and customers is desirable. Consequently, for efficient sensory evaluation management in the digital environment, individual solution strategies with a high practical benefit must continually be developed.
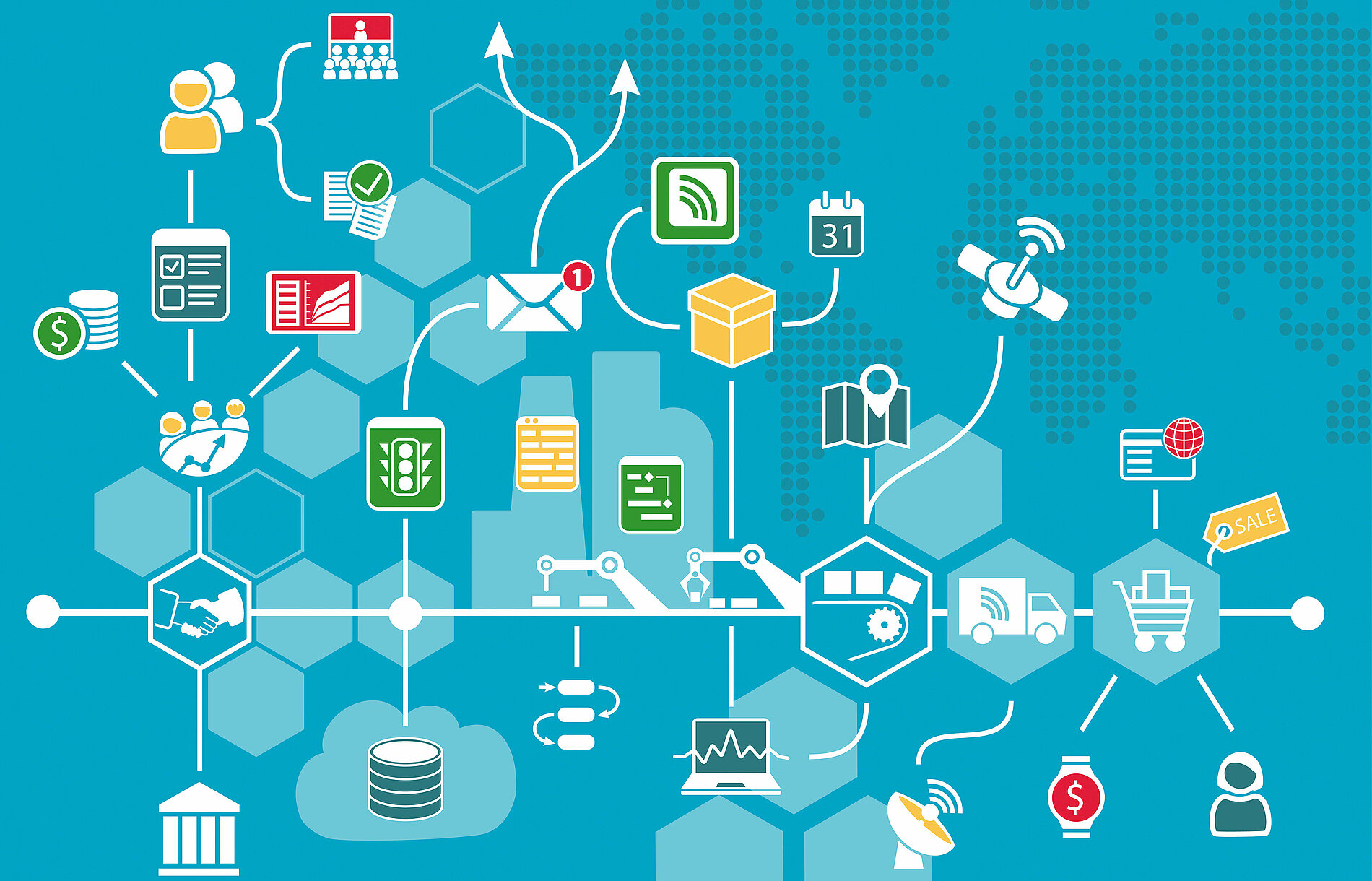
1. Background, definition and goals of Industry 4.0
The term Industry 4.0 stands for the fourth industrial revolution and was first used in Germany in 2012. This is to express that after mechanisation, electrification and automation, digitalisation and networking will now follow. By connecting people, objects and systems, dynamic, real-time-optimised and cross-company networks are created along value-added chains with the aim of increasingly optimising the organisation and control of processes. Unlike previous technology-driven upheavals, this time it is not about a single technology, but rather the linking of different methods and technologies from information and communication technology.
To implement Industry 4.0, a company individually combines methods, technologies, data, models, services and processes. Optimisation can therefore start both within different company areas and at the interfaces to customers, suppliers or partners. An important prerequisite for the successful implementation of Industry 4.0 elements are transparent, efficient processes and structured data management. However, it is always necessary to clarify the relationship between expected market advantages and risks in connection with the complexity of the system (see Figure 1).
Experience has shown that various hurdles must be overcome in the organisational embedding of an increasingly complex information technology. New know-how needs to be learnt and existing processes need to be questioned in terms of their efficiency and targeting, so that routine procedures can be modified or broken if necessary. Due to the flood of information and the often lacking knowledge about the digital world, SMEs are particularly challenged. How should one start in specific terms? Do I need a vision and strategy first? What technologies do I use? At the beginning there are countless unanswered questions, which greatly increases the uncertainty. There is a danger that the issue will be postponed or only tackled half-heartedly. However, a targeted approach to the digital transformation is urgently needed in order to remain competitive in the future and to continue to be part of the increasingly complex value-added chains.
2. Digitalisation along the value chain: Focus on consumers and the food industry
In the food industry, there are many approaches to digitalisation along the entire value chain, from purchasing to logistics, production, quality assurance, marketing, sales and service.
Digital integration in marketing and distribution is already well established. How will consumers shop in the future? How will they eat and evaluate? These questions are not only aimed at changes in consumer behaviour, but also at the relationship between consumers and the market. Customers are increasingly using social networks and rating platforms where they can publicly share their assessment and criticism of companies and their products for everyone to see. The challenge for sellers and manufacturers is therefore to provide information about their products on the Internet as transparently as possible.
With the help of Big Data, companies know more about their customers than ever before, and this knowledge will grow with increasing digitisation and data collection. This enables companies to optimise consumer experiences, products and services in the interest of the consumer, to increase customer satisfaction and ultimately to increase their turnover.
In the relationship with the consumer, a company operating in the food industry can convey additional credibility and security through the correct interpretation of Big Data. Especially when the digital transformation is also implemented in the areas of quality assurance and services. Consequently, the topics of digitalisation are not only of high urgency in the food trade, but also among food manufacturers. They are therefore more often on the agenda of management meetings and priority projects of the management.
3. Digitalised quality assurance in the corporate process
With the focus on providing consumers with optimal product quality and meeting customer needs in the best possible way, the digitalisation of quality assurance has already been partially implemented or at least addressed in most food companies. Database-oriented application systems can efficiently support sample processing and store the accumulating large amounts of data in a structured, evaluable form. For example, LIMS (Laboratory Information and Management Systems) realise a seamless and automated process chain – from the registration of incoming samples to the specification of the examination parameter and scope and furthermore, from the data acquisition of analysis results to reporting or economic evaluations in the laboratory. When deciding on an LIMS, it is seldom only rationalisation, i.e. saving time and money, that is decisive, but also the possibility of recognising quality problems at an early stage and being able to counteract them.
These systems for digitising quality assurance ideally have interfaces to other in-house data systems or to higher-level planning systems (ERP systems).
For optimal quality and high consumer acceptance, systems must measure meaningful and relevant data. What are the critical properties for the consumer, which characteristics are preferred and how much deviation from the target value is permissible? These specifications must be defined by marketing and specified by quality assurance with corresponding analytical values. It is determined which analytical parameters and process parameters are required so that the manufacturing process is automated as far as possible and can be controlled in real time (see Figure 2). The process is monitored so that the critical parameters are always met. Real-time control allows deviations to be detected early and corrected immediately before they are out of tolerance. More controls are carried out directly in production and no longer in the laboratory. For example, infrared measuring devices can be used to measure fat content and dry matter, as well as the quality of other essential ingredients. In case of deviations, corrective actions are taken immediately, for example, by adding fat or water. Ideally, this is done fully automatically, but it can also be done manually in some cases.
In the area of appearance and texture/haptics, real-time controls can largely regulate the process for consistent product quality. These physical sensory stimuli, or product characteristics such as colour intensity, spotting, crispness, moisture or creaminess, are measured with sensors and digitally controlled. In contrast, the chemical stimuli relevant for the perception of smell and taste are currently still difficult, or in some cases impossible to determine by means of real-time controls due to their complexity. A process-integrated, continuous measurement of the test characteristics aroma and taste is currently in most situations just possible by means of end product control. But even this primarily human-sensory quality assurance can be digitalised.
4. Importance of digitalisation for sensory evaluation in the food sector
In sensory market research as well as in sensory quality assurance, a digital sensory management system tailored to operational processes and procedures offers many advantages over conventional “analogue” procedures. Of these, the time saved and errors reduced by the elimination of traditional paper-based inspection sheets and result reports represent only a part. The QA managers of the daily tastings, as well as internal clients or external customers of sensory-analytical services, benefit from the higher efficiency and transparency of the sensory test results determined and from the prompt data transfer via networked IT systems. In addition, there is electronically based documentation of examiner performance, which provides those responsible for sensory evaluation with a good database for targeted ongoing examiner selection and examiner or panel qualification. The human being is in this process the analytical instrument for measuring the sensory properties and monitoring the quality of the previously defined parameters.
What are the advantages and critical success factors of digital sensory evaluation technology and what hurdles must be overcome to achieve this? According to Dr Claudia Franke, Managing Director of the consulting company SIREQUA, with 18 years of R&D and QM management experience at well-known food producers, the digitalisation of the sensory evaluation process in the food sector has multiple advantages. In addition to time and cost savings, the focus is on the neutrality of sensory tests, efficient and more detailed evaluations of sensory results and a paperless archive.
In the digitalisation of food sensory analysis, each participant usually evaluates his sample individually without exchanging information with other participants. The results of all participants are then compiled into a joint results report. On the other hand, in the traditional approach with documentation on paper, the participants often exchanged comments among themselves and a tasting manager compiled the tasting report from the sum of the comments. Neutrality was not always given, especially when participants from different hierarchies were present. Often, personal preference and sensory quality assessment or devaluation were also mixed in this type of tasting. As a result, the original question was not always clearly pursued and the actually desired analytical and objective sensory quality assessment was undermined.
The tasting reports were filed away and were often difficult to find again when questions arose later. In the digital world, however, the tasting reports are stored and, provided a descriptive name has been chosen, can be easily found by anyone. As all data of the tasted products, the tasting process itself and the possibly formulated corrective action, are available in a database, various evaluations can easily be made. For example, trends can be identified or actions can be tracked that affect both the analysed product itself and the involved testers, their qualifications as well as their sensory performance during the test.
The basic prerequisite for digitisation is, of course, a stable and fast IT network and user-friendly software that can ideally be used from anywhere via smartphone, tablet or PC. The security of the stored data must always be taken into account and guaranteed. As current practical experience shows, after the first application, the advantages of digitalisation will also convince participants who previously and actually preferred to work with paper.
„Life was made tremendously easier“ – case study: Emmi Fondue AG, Switzerland
Emmi Fondue AG, a Swiss food producer with 130 employees (see Figure 3), digitalised its sensory QA process with the SensoTASTE software system more than 4 years ago. The internal sensory management system with 1 administrator, 4 tasting managers and an expert team of 13 users is used for daily QA tastings, product developments and sampling.
What has changed through this digitalisation? The spontaneous feedback from Simon Blaser, Project Manager for Innovation/Application, was: “Life was made tremendously easier!” The credibility of the quality assurance and its approval process had increased again and the discussions with the management were significantly reduced. The simple, transparent traceability and the clearly understandable reports for all parties involved are a valuable benefit.
The critical success factors for Simon Blaser are: “A defined evaluation, the transparent and “clean” data situation, higher efficiency and the speed achieved”. Compared to the previous analogue processing, the benefits of digital implementation in terms of structure and overview are great. The automatic report generation and the transparent information (from the individual results to the final findings) also show less subjectivity.
In the introductory phase, certain hurdles had to be overcome, which was met with internal scepticism about “the change from analogue to digital”. The initial effort to standardise the processes and documents, i.e. among other things the definition of the process parameters (references, target values and product profiles) and the inspection tasks or protocols, was considerable. Because the entire sensory evaluation process was also optimised in connection with the software implementation. New audit forms and checklists were created and adapted to internal needs. An important requirements was that the data from other systems (e.g. chemical laboratory parameters) did not have to be re-entered. The connection with the existing data systems worked out very well. The paperless sensory management system, which was tailored to the company’s processes, gained a high level of acceptance among QA test managers, developers and the management soon after its introduction.
Through trend analyses as well as storage tests, evaluation criteria can now be compared over longer periods of time and seasonal tendencies can be recognised and interpreted. The large, clearly structured data material now enables more informed feedback to suppliers or customers and leads to more consistent quality.
5. Software offers for the digitalisation of sensory evaluation processes at a glance
If the decision is made in the company to digitise food sensory evaluation technology, there are various implementation options and software programs of different categories, each with varying application focuses. It is important to determine which areas of the sensory evaluation process in the company are to be digitalised and how networking to other company data can be realised. Sensory evaluation is a cross-divisional activity, so that comprehensive data can be generated in the course of sensory testing in quality assurance, product development and marketing, i.e. market research. The following list presents four main, different software categories that are currently offered on the market:
a) Software programmes with a focus on individual projects and sensory research
There are some software tools specialised in sensory testing in general and sensory research in detail, such as FIZZ, Compusense or Red Jade®, among others. These solutions have extensive applications in both analytical and hedonic methods (acceptance and preference tests) and their statistical evaluation. With this, both simple and complex projects in sensory evaluation with different questions and using different methods (also quick methods such as Sorting, Napping®) can be mapped and digitally controlled. In addition, they allow subjective consumer impressions to be linked with objective sensory profiles. These methods are very well suited for sensory product research projects, for building a descriptive panel or for multidimensional preference mappings.
But these software tools are currently less useful for standardised, ongoing tasks that focus on sensory analysis in quality assurance. This consists of data management of samples and products, storage tests, trend analyses over longer periods of time or on an ongoing basis, action management and connecting with other company processes.
b) Software programmes with a focus on sensory consumer research
General consumer survey tools, such as Questback, Rogator or Survalyzer, have advantages in the area of target group screening and in programming more complex questionnaires. These tools are specialised in many different questionnaire items, and therefore allow a high flexibility in questionnaire design. When using standardised questionnaires, they are not very automated. Often, these systems have a panel administration to draw random samples of testers for any panel or to send invitations or reminders to the pre-selected panelists. However, they have neither sample management nor sensory-specific evaluations such as difference tests or storage tests.
c) Software programmes with a focus on product data
Conventional product databases, such as PIM (Product Information Management) or LIMS (Laboratory Information Management Systems), have extensive product, sample and project databases. They also ensure the transformation of the data to other internal systems. However, these software programs only have very limited sensory-specific functions and few possibilities for the digital integration of sensory processes, e.g. questionnaire design for sensory tests and for statistical evaluations.
d) Software programmes for sensory management focussed on ongoing, routine sensory evaluation projects in practice
The digitalisation of sensory evaluation, e.g. through the software application SensoTASTE, covers the needs of regular and standardised tastings very well – either in quality assurance, product development or marketing. After an initial implementation of the current company-specific processes around food sensory evaluation, the projects within sensory analysis are planned and evaluated with minimal effort. The high level of automation allows questionnaires, panelists or testers, rating scales and samples to be automatically assigned to the tastings “at the touch of a button”. After the sensory evaluation, the statistical evaluation as well as the report is immediately generated and the data is linked to other operating systems. Statistical functions and multidimensional evaluations (multivariate applications, multidimensional scaling) are less pronounced.
The requirements and needs of a digitalised sensory evaluation process or sensory management are manifold. Data management that maps different, often routine and standardised sensory evaluation projects of the company or department should include the preparation, collection, processing, evaluation and interpretation of the data as well as data connecting and data management.
The SensoTASTE software system covers many of these needs. It also contains clear product, sample and project databases with input boxes which can be customised and it has a flexible questionnaire design. Figure 4 shows an example of the digitalised sensory evaluation process mapped by SensoTASTE. It also illustrates how the basic process can be supplemented by other useful modules. The modules of the basic process are shown there as blue boxes and supplementary modules as green or yellow boxes. This sensory evaluation data management focuses on efficiency, flexibility and transparency.
Project planning is followed by the creation or selection of questionnaires, the recruitment, selection and invitation of panelists, and finely the sample management.
The decentralised data collected in the course of the tasting is received via “mobile clients”, ideally via tablet PCs or smartphones. The SensoTASTE software then links the Mobile Client of the accessors with the Admin Client for administration, and therefore provides the base for creating individual result reports at the “click of a mouse”. The entire process runs paperless, without media breaks, and is therefore significantly less prone to errors. The mobile product evaluation is automated and responsive for all input devices, the evaluations are timely and the data storage is structured. Figure 5 illustrates the main steps of an digitally supported assessment with SensoTASTE.
The basic process shown in Figure 4 can also be supplemented with useful modules. For example, through actions management with a traffic light system or through a product presentation on the web by means of displaying the profiling as a spider web diagram. Interfaces to ERP systems (e.g. SAP), laboratory information systems (LIMS) or other product information databases can be easily implemented. In the user administration, testers are created and roles and authorisations are assigned. The Reporting Pro module contains additional evaluation options, such as participant and panelist analyses, usage statistics and product trend analyses. The QA sensory evaluation test module contains predefined test sheets for difference tests and storage tests.
Depending on the requirements, the in-house version with hosting at the customer’s premises or the web-based cloud version with hosting at SensoPLUS can be selected. The in-house version allows simpler connections to in-house software components, such as Active Directory or ERP systems. The web-based version makes the user less dependent on the in-house server and the system can also be used outside the intranet via the cloud. With both versions, no installation on the end devices of the test leaders and testers is necessary, as the application can be accessed via a web browser, such as Internet Explorer, Safari or Chrome.
Once loaded onto the mobile client, test protocols can also be completed offline, i.e. without a connection to the server (see Figure 6). The data is synchronised as soon as the device is online again. This means that sensory evaluation tests can also be carried out at locations without intranet/Internet.
For the introduction of the sensory evaluation software, SensoPLUS sets up a mandate for the customer and carries out internal training, during which the required templates are set up at the same time. After the WiFi network has been set up by the company’s own IT department and the terminal devices have been configured, the reports may still need to be adjusted. A standardised implementation can be realised within 1-2 weeks.
Every company has the possibility to optimally align the data management process with its own procedures, so individual solution strategies can be created through customising. Report formats, checklists and interfaces are therefore installed specifically according to user needs (see Figure 7: Automatically generated pdf report, Emmi Fondue AG; example of customising: Colouring can be used to support statements of results so that they are immediately understandable for the report recipient).
6. Digitalisation throughout the product life cycle
From the idea to the launch and right up to the monitoring of a product after its launch, several sensory tests and stages are run through. Many of the tests carried out in the process take place internally in the companies. Structured sensory processes, suitable sensory evaluation software and digital connection of the systems involved enable efficient processing of the tasks that arise within the company.
In the innovation process and in the benchmark test, however, the match between the product profile and customer needs is the decisive factor for product success. Regular consumer feedback is therefore essential in the ongoing quality assessment of products. Here SensoPLUS provides support product or concept tests in which prototypes or products from the existing range are tested by a target group panel. With the two methods of
SensoPRODUCT and SensoCONCEPT for the customer research, many solutions are developed in the first creative phase. These ideas are then systematically and objectively analysed. In the further development of the innovation and in benchmark test monitoring, the consumer and his/her product assessments are always in focus in order that the product concept and the sensory profile can be controlled so that it meets the customer expectations in the best possible way.
The SensoPLUS services for companies in the food sector is complemented off by another software tool of interest to corporate practice, SensoCHECK. With SensoCHECK, the entire quality assurance process is handled efficiently. The on-site recording of all findings and actions, as well as the automatic data transfer and data exchange with ERP, LIMS and CRM systems reduce the workload enormously. SensoCHECK can also be optimally used for inspections and audits. Standardised checklists for HACCP, BRC or IFS can be mapped in the system for this purpose. Findings can be supplemented with photos or drawings for illustration. Due to the high level of transparency, the corrective actions are implemented consistently. The quality manager organises and consolidates less and the production managers are better informed in a timely manner and overall.
7. Outlook
The connecting of the various systems will become faster and faster in the future, automation will continue to increase and the exchange of data will improve. In terms of systems technology, more and more is being moved to clouds, so that in future internal systems will have an even stronger connection to an encrypted cloud environment than before. It would even be possible for companies to have no internal servers, little in-house software development and only hardware terminal devices in the future. Like every trend, this digital development also triggers counter-movements. The new data protection regulation and the increasingly important issue of data protection among consumers are just a few of them.
The technical system will be able to take over more and more work from humans in various areas. This also applies to the important area of food sensory analysis. In this way, samples can be captured via scan codes, as an image or via voice recognition and immediately linked to all relevant data. Whatever is possible is captured by instrumental measurements in real time. In sensory evaluation, this includes the test characteristics of appearance, texture and presumably soon also aroma. These data are digitally linked with the still necessary human sensory assessments. After the test planning, the person “only” has to taste and the project manager then of course ultimately interprets the result data.
Digitalisation has brought disruptive changes in many areas in recent years, which have fundamentally altered consumer behaviour and market mechanisms. Well-known examples include the enormous growth and development of platforms such as Amazon, Uber, Airbnb, etc. Such striking changes would also be possible in sensory evaluation technology. Sensory clustering, consumer feedback apps and monitoring of emotions are already a topic and will bring food companies ever closer to consumers and their individuality in the future. Digital solution approaches, such as the use of big data and artificial intelligence, also open up further new horizons.
8. Selection of software programmes in connection with sensory evaluation
With reference to the categorisation of software programs in connection with sensory evaluation, a selection of software offers is compiled below. This provides the basis for further individual research and, if necessary, personal contact.
Software Program | Focus | Website |
SensoTASTE | Sensory management | http://www.sensoplus.ch/sensosoftware/ |
FIZZ | Sensory research | https://www.biosystemes.com/ |
Compusense | Sensory research | https://www.compusense.com/ |
RedJade® | Sensory research | http://redjade.net/ |
Questback | Consumer research | https://www.questback.com/de/ |
Rogator | Consumer research | https://www.rogator.de/ |
Survalyzer | Consumer research | http://www.survalyzer.com/de/ |
Literature, references:
- https://www.swissmem.ch/de/industrie-politik/industrie-40-digitalisierung.html
- A. Ternès, I. Towers & M. Jerusel; Konsumentenverhalten im Zeitalter der Digitalisierung;
Springerfachmedien Wiesbaden, 2015; S. 22-23 - http://www.sensoplus.ch
- Emmi Fondue AG, Simon Blaser, Projektleiter Innovation/Applikation; Lizenzträger von SensoPLUS
Frau Dr. Claudia Franke, Geschäftsführerin Firma SIREQUA
Kontakt
DLG-Fachzentrum Lebensmittel • Bianca Schneider-Häder • Tel.: +49 (0) 69 24 788-360 B.Schneider@DLG.org