- 1 Introduction
- 2 Aspects of the efficient and safe application of plant protection products (PPP)
- 2.1 Forms of plant protection products
- 2.2 Tank mixtures
- 2.3 Influences on the effectiveness of crop protection agents
- 3 Use of sprayers
- 3.1 Personal protective equipment
- 3.2 Protection through driver’s cabs
- 3.4 Cleaning
- 4 Maintenance
- 4.1 Winter storage
- 4.2 Preparation for implement inspection
- 5 Literature
- Authors
1 Introduction
This Expert Knowledge Series pamphlet is part of a series of DLG Expert Knowledge Series pamphlets dealing with the complex issue of crop protection agent application.
The Expert Knowledge Series pamphlets published so far in this series deal with:
- Information on the storage of crop protection agents (DLG Expert Knowledge Series 452 ‘Lagerung von Pflanzenschutzmitteln auf dem landwirtschaftlichen Betrieb’ (Storage of crop protection agents on farms) [1])
- An overview of legal framework conditions (DLG Expert Knowledge Series 409 ‘Correct crop protection – things to check before you start’ [2])
- Special considerations concerning water protection (DLG Expert Knowledge Series 413 ‘Pflanzenschutz ohne Wasser zu gefährden’ (Crop protection without endangering water) [3])
- An overview of the state of the art of modern crop protection sprayers (DLG Expert Knowledge Series 467 ‘Crop protection sprayer technology’ [4])
This Expert Knowledge Series pamphlet is focused on notes, recommendations and information concerning the use of crop protection sprayers.
2 Aspects of the efficient and safe application of plant protection products (PPP)
The plant protection products industry provides farmers with a wide range of different, highly-effective crop protection agents to enable them to counteract possible reductions in crop yield and/or quality due to weeds, insect pests, fungal pathogens or rodents. In addition to PPP’s for various indications such as fungicides, insecticides or herbicides, various product forms are also available. For instance, crop protection products are available in both solid (granules, powder, etc.) and liquid form. Farmers are therefore constantly faced with the task of selecting the right product or product combination for their requirements (pathogen, crop, development stage, possible mixing partners, statutory regulations) from the variety of products on offer.
Besides the aforementioned biological requirements, the use of PPP’s is determined by a variety of additional influencing factors. These include the application technology (e. g. sprayer type, type of agitator), tank mixing partners (e. g. crop protection agents, fertilisers, additives) and also specific factors such as the formulation type of an agent, mixing tolerability, quantity and quality of water, for instance. Optimum PPP application requires the ideal interaction of the influencing variables involved. The principles for the implementation of good professional practice in crop protection describe the basic principles to be observed.
2.1 Forms of plant protection products
The effect of plant protection products is based on the activity of the effective substances contained in them; these are called active substances and have a specific effect on different target organisms. Consequently, they are appropriately allocated to the group of fungicides, herbicides, insecticides, acaricides or growth regulators, etc. However, directly applying the active substances onto a crop or (grass) weeds very rarely leads to the desired effect. The active substance first has to be formulated as a plant protection product in order to optimally ensure its biological effectiveness, storage stability and handling capability for the user.
The active ingredients itself determines which type of formulation is possible due to its characteristics. The solubility and stability of the active substance in solvents such as water are important criteria, for instance. A distinction can generally be made between three major groups, which are identified using corresponding formulation codes:
- Solid formulations (e. g. WG, WP, SG)
- Water-based formulations (e. g. SC, SL)
- Solvent-/oil-based formulations (e. g. EC, DC, OD)
A full overview of all international codes can be retrieved from CropLife International [5].
2.2 Tank mixtures
Tank mixtures are used in farming, for instance, to achieve an extended spectrum of effect, to prevent pathogens from developing resistances, to forgo operations or because products can only be mixed prior to application due to certain physico-chemical characteristics.
Each formulation type has its own specific characteristics. These characteristics have to be observed in the case of tank mixtures, which results in a corresponding mixing sequence for the products. The following basic principle can generally be assumed: ‘from solid to liquid (with the exception of fertilisers) – from hardly soluble to readily soluble’.
The following approach acts as a basic concept for preparing tank mixtures in crop protection:
- Water (approx. half of the sprayer’s volume)
- Set the agitator to medium intensity
- Add anti-foaming agent if necessary (see specific product information)
- Fertilisers, micronutrients (solid)
- Solid formulations (WG ➝ WP ➝ SG ➝ SP)
- Water-based formulations (SC ➝ CS ➝ SL ➝ ME)
- Solvent-based formulations (SE ➝ EW ➝ EC ➝ DC ➝ OD)
- Residual water
- Excipients and additives, depending on their formulation form
2.3 Influences on the effectiveness of crop protection agents
In addition to the crop protection agents, water is a crucial factor for successful application. Water is both the carrier substance and the solvent for all tank mixing components in a spraying liquid. In order to produce a homogeneous and applicable spraying liquid, the water that is used should always be both clean and of a sufficient quantity (water application quantity in l/ha) in order to completely dissolve the products. Sand and other impurities easily block the filters and can foster the binding of active substances (usually visible in the form of precipitation or flocculation). The hardness/pH value of the water should additionally be known, and attention must also be paid to the factor of the water temperature. This enables the avoidance of difficulties caused by very hard water or very low water temperatures with individual products (around 10 to approx. 20 °C can be regarded as the optimum water temperature for the majority of applications).
The water hardness is geogenically related and therefore reveals a geographical distribution corresponding to the characteristics of the respective soils and/or aquifers. The basic values for determining and evaluating water hardness are above all the magnesium ion, calcium ion and hydrogen carbonate contents. The hardness of water can be determined on the basis of this data. The hardness of water tends to increase along with increasing contents of the aforementioned ions. Additional values from a water analysis (e. g. iron content, manganese content) can also provide very helpful information for avoiding problems.
Besides the water temperature and hardness, discussion is also often focused on the pH value of the water. The influence of the pH value on the dissolution or mixing behaviour of a product is relatively low compared to some of the other factors. The majority of crop protection agents are adequately pH-stable and are only influenced by the pH value of the water to a minor extent. Depending on the water hardness, the pH value is usually between 6.5 and 8.5. Even at high pH values, the risk of degradation of an active substance molecule due to alkaline hydrolysis only exists in a very few exceptional cases. As with high water hardness, metal ions and/or other cations pose a potential risk of binding (complexation, precipitation) for individual active substances at a high pH value.
PPP’s may only be used in the application areas set down in the marketing authorisation and under the application conditions defined there (e. g. indication/crop, maximum permissible application quantity, conditions) [6]. When storing PPP’s, it must be ensured that the basic requirements are met, e. g.: locked room that is not accessible to unauthorised persons, clearly arranged, cool, well ventilated, protected from frost, etc. [1]. It should additionally be noted that, besides the legally specified marketing authorisation duration, crop protection agents are also subject to a defined shelf life/warranty period and accordingly have to be checked on a regular basis.
In tank mixtures, the ratios of individual mixing partners to one another can influence the mixing behaviour/mixing compatibility. Commonly used mixtures are usually tested conscientiously by the plant protection product manufacturers. Corresponding recommendations and notes should be observed. If these are not available, a small batch (10 litres) of the chosen tank mixture should be tested in advance. Depending on formulation type (solid – liquid, water-based – solvent-based), the products take a certain time to dissolve completely in water. This must be taken into account when preparing tank mixtures. In addition to the correct sequence of the products depending on their formulation type, each further product should only be added once the previous one has dissolved completely. The use of an agitator set to medium intensity is advantageous to support complete dissolution and subsequently keep the spraying liquid in a homogeneous condition. Any problems that arise must be eliminated before the next product is added. Under certain circumstances, non-ionic wetting agents and water can help to dissolve and eliminate precipitation and sediments. ECs, oils, certain micronutrients and liquid fertilisers may prove helpful in individual cases.
Many problems only occur after filling the sprayer multiple times or after idle times. As a result of this, tank mixtures/spray liquids should be prepared directly prior to use and idle times should be avoided wherever possible. Properly and thoroughly cleaning the spraying machinery and equipment each time after use is the simplest and most reliable method for preventing possible problems and surprises the next time they are used.
3 Use of sprayers
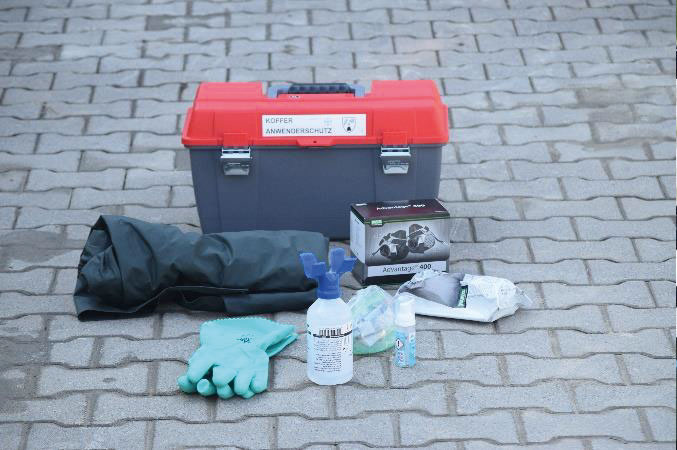
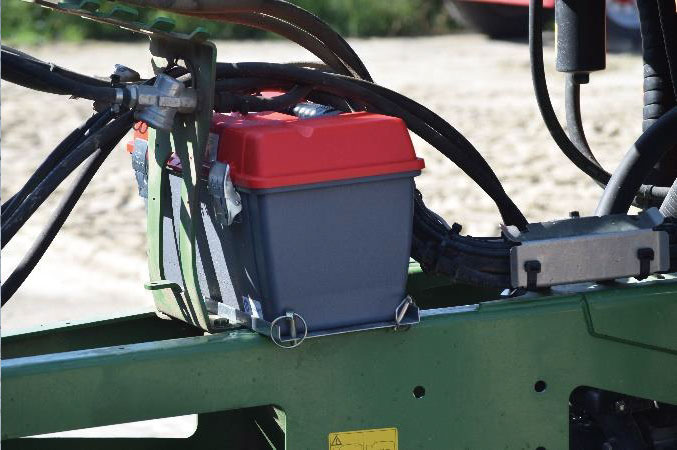
3.1 Personal protective equipment
On authorisation of a PPP for marketing, the BVL (German Federal Office of Consumer Protection and Food Safety) bindingly specifies the use of personal protective equipment (PPE) (Figure 1) individually for each PPP. If the user forgoes the specified PPE or uses PPE that is unsuitable or no longer suitable due to damage, contamination or ageing processes, achieving the necessary level of protection is not ensured. An unjustifiable health risk is then not ruled out.
A list of certified work clothing, suits for protection against PPP, arm coverings and protective gloves (crop protection) that meet the requirements of the BVL guideline can be found on the BVL website at www.bvl.bund.de/psa [8].
Handling PPP’s encompasses the following activities:
- Handling of concentrated agents to prepare for application (e. g. preparation/mixing of the spraying liquid, filling the sprayer)
- Handling of ready-to-use agents (e. g. granules for application, bait, pheromone dispensers)
- Treatment of seed and handling of freshly treated seed
- Treatment of harvested crops and handling of freshly treated harvested crops (e. g. storage of potatoes)
- Application of the PPP with the aid of any application technology
- Contact with freshly treated plants and surfaces on the cultivated area during application
- Cleaning the sprayer that have been used including systems for treating seed and harvested crops, containers and tractors
- Disposal of the empty PPP containers
- Disposal of PPP’s/residues that are no longer approved or are subject to mandatory disposal.
3.2 Protection through driver’s cabs
Tightly closing driver’s cabs can effectively protect users from exposure during the application of crop protection agents, particularly due to spray mist. The protective effect is dependent on the technical design and handling of the various cab types and can be subdivided into categories with various levels of protection (Figure 2).
Figure 2: Categorisation of cabs
(source: Kramer, modified according to BVL technical bulletin, 8 January 2020)
Cab type | Protection against | Technical requirements | Certificates | ||
Dust | Aerosols | Vapours | |||
Category 1 | No protection level defined; open cab or half-cab | None | |||
Category 2* | * | Tightly closing cab with air conditioning system and supply air filtration | None | ||
Category 3 | Requirements pursuant to EN 15695-1 and -2** | EN 15695-1 and -2 | |||
Category 4 | Requirements pursuant to EN 15695-1 and -2*** | EN 15695-1 and -2 |
* Suitable within the meaning of these regulations for the substitution of PPE: cabs certified in accordance with EN 15695-1 and -2, also cabs classified in category 2 and cabs that meet the specified technical requirements
** In addition to category 2: air exchange rate > 30 m3/h, indication of cab positive pressure, leakages < 2 %, fine particulate filter (HEPA filter)
*** In addition to category 3: activated charcoal filter with protective effect against gaseous substances
No protection | Protection level | *Still currently suitable |
3.3 Filling
Prior to application, the various crop protection agents must be diluted with water. With the usual application quantities of 150 to 600 l/ha, very large quantities of water are required in a short space of time to fill large crop protection sprayers. The public or the farm’s own water supply is therefore often insufficient to fill the spray tank directly without long waiting periods. Efficiency during spraying can be significantly increased due to reduced waiting times for filling by storing the water in spraying water tanks in advance (Figure 3).
Before and during spraying, these tanks are filled using floater-controlled valves and then emptied into the spray tank using the largest possible pipes or hoses. If the storage or buffer tank is positioned so high up that its water level is always higher than that of the spray tank, a pump can often be forgone for filling. Low pressure and low water drop heights reduce foam formation. However, it must be ensured during both direct filling and filling from the storage tank that the water lines are not connected directly to the spraying liquid.
If the field-to-farm distances are long, it can prove sensible to transport the water or the spraying liquid to the edge of the field using a mobile transport tank and to fill the sprayer there (Figures 4 and 5).
This significantly increases the sprayer’s efficiency, particularly on large farms with numerous workers.
When transporting undiluted crop protection agents by road, it must be remembered that the ‘Regulations for the Conveyance of Hazardous Goods by Road’ must be complied with.
The PPP’s are usually introduced into the sprayer via the induction bowl. When doing this, it must be ensured that the sprayer is half full of water before beginning to dose the agents. The agents dissolve better as a result and flocculation is prevented. Of course, the correct sequence when dosing the agents is also crucial in this process (see 2.2).
The classic removal systems such as e. g. Farmchem, EasyFill, AgriFill, Polmac, QuantoFill M and others can be used with the filling systems. In addition to smaller containers (1 l – 20 l), large containers can also be pumped or dosed into the sprayer. Individual systems support the farmer with a filling computer, which undertakes precise measurement and filling into the sprayer.
The trend in filling systems is shifting to completely closed transfer systems (CTS) such as the EasyFlow or EasyConnect systems, for instance, which virtually rule out contamination of the user and the environment (Figure 6).
With these systems, it must be possible to attach and remove the components in dry form. With the EasyFlow M system, any foil seal that is present (see Figure 6, right) is opened on the canister and also cleaned, but remains securely on the canister. The tank adapter can also be flushed accordingly when removing a partial quantity.
If the canister is uncoupled again, compulsory resealing by the adapter must take place beforehand (simple rotation), as the connection cannot otherwise be released.
3.4 Cleaning
After use, the interior of the sprayer should be cleaned immediately. Carefully cleaning all parts that conduct liquid when changing the crop protection agent is a must, particularly when dealing with sensitive crops, in order to prevent damage to the crop. However, cleaning should also be carried out immediately on the field in the case of application with numerous mixing partners in order to avoid deposits. To do this, the technical residual quantity contained in the tank, the pump and the lines must be diluted in a ratio of at least 1:10 and applied over a wide area. Tank cleaning nozzles installed in the tank additionally help to clean the main tank directly after application. It is important that all the sections and also the return hoses are flushed through with residue-free water. What is called the splitting method is appropriate for this. In this process, the sprayer’s stock of clean water is conducted into the sprayer in three stages via the internal cleaning nozzle. It is then circulated and applied on the field. Alternatively, internal cleaning is carried out quickly and efficiently with electronic cleaning programmes or by means of continuous cleaning system. In the continuous cleaning system, an additional pump between the fresh water tank and the internal cleaning nozzle ensures that the cleaning process can be carried out very quickly (in less than 10 minutes) and also comfortably from the driver’s seat. However, the most important aspect is that cleaning is carried out directly after application, as this achieves the greatest cleaning success.
The exterior of the crop sprayer should also be cleaned on the field, as a specially equipped washing station, in which all of the washing water is collected and disposed of in an environmentally sound manner, must otherwise be available on the farmyard (Figure 7).
The sprayer should be cleaned on a sufficiently large, untreated strip on the field. The necessary technical equipment, such as washing water tanks, hose reels and spray lances, are available as additional equipment from the implement manufacturers. A sufficiently large fresh water tank (approx. 10 % of the rated tank volume) is available on the sprayer and necessary for cleaning the sprayer and the tank and for the canister rinsing facility. If the entire fresh water tank is required for interior cleaning, a separate tank can also be carried along in the front hydraulics (Figure 8). This can also be combined with a battery-powered high-pressure cleaner.
4 Maintenance
4.1 Winter storage
First of all, the exterior of the sprayer must be cleaned with a washing brush or a high-pressure cleaner at a washing station or on a manure slab with a run-off into a manure or slurry pit. PPP’s residues must be prevented from entering the sewer system or surface waters under all circumstances. This is then followed by thorough interior cleaning. Depending on system, this is carried out continuously or in stages; cleaning agents developed specifically for this purpose are recommended. Alkaline milking machine cleaning agents can also be used. However, this is dependent on the PPP’s that are used. Besides the spray tank, the induction bowl and the agitator must not be overlooked. Deposits must be removed manually if necessary. The cleaning fluids that are incurred must be output onto the field. All removable parts such as nozzles and filters are cleaned separately. Inexpensive ultrasonic cleaning devices have also proved suitable for this; in combination with washing-up liquid, they are also able to effectively remove stubborn coatings in filters and nozzles. After drying, all moving parts such as the PTO, pivot joints and hinges on the boom must be lubricated, and metal parts must be sprayed with an anti-rust agent to prevent a rust film. The hoses must also be checked and treated with talcum powder or another form of rubber protection so that they remain flexible.
Once the sprayer has been completely emptied along with all of its lines, nozzles, fittings and pumps, it should be either blown out with compressed air or, if permitted by the sprayer manufacturer, protected against frost with an antifreeze such as Glysantin. In the latter case, it must in turn be ensured that all lines are filled up to the nozzles. One advantage of the antifreeze method is that seals and diaphragms do not dry out. The antifreeze solution can be drained in the spring and stored in suitable containers for reuse.
While UAN prevents freezing when used as an antifreeze, it is aggressive towards metal parts and rubber seals. It is best to remove the suction and pressure filters, pressure gauge and computer and to store them in a frost-free room. The cleaned nozzles can be stored in a bucket of water. The sprayer should then be parked in a dry location that is protected from direct sunlight so that the plastic parts do not become brittle.
4.2 Preparation for implement inspection
Since 2013, crop protection implements are required to undergo an mandatory sprayer inspection every three years. A suitable inspection appointment at a specialist workshop should be arranged for this in good time. It is generally important not to lose track of when the sticker is due to become invalid. If this is not noted on the sticker – first (up to 30 June) or second (up to 31 December) half-year – the inspection protocol should be referred to.
To ensure that the inspection proceeds smoothly, the crop protection implement should be prepared according to the following list:
- Thorough cleaning of the interior and exterior of the implement – it is best to clean it on the field and discharge the washing water there. If an uncleaned implement is presented, the farmer must anticipate having to present his sprayer again after cleaning it or being invoiced for cleaning
- If the sprayer is presented for inspection directly after the winter, do not drive to the workshop with antifreeze in the pump
- Clean all implement filters beforehand
- Remove nozzles and clean them (with a soft brush or compressed air). In the event of extreme soiling, pre-cleaning can be carried out using an ultrasonic bath
- Check the non-return valves and diaphragms with the implement running. After shutting off the spraying line, the nozzles may continue to drip for max. five seconds
- If the nozzles ‘flutter’ severely during spraying, check the oil level of the implement pump’s compensation tank and the air pressure in the air compensation tank. The pressure should be slightly lower than the spray pressure
- Check the sprayer for leaks. Tightening hose clamps or threaded connections often suffices to stop leaks
- During the inspection, make sure that long injector nozzles (ID, IDN, TD, AI, AVI, AVI Twin, HiSpeed, etc.) are tested at approx. 5 bar and compact injector nozzles (AirMix, IDK, IDKN, MD, IDKT, etc.) or standard flat fan nozzles (XR, LU, SD, etc.) are tested at approx. 2 to 3 bar (standard pressure!)
- Wherever adjustment options are available on the boom, it should be aligned on a flat surface if necessary
- Drive the sprayer to the inspection with sufficient water (tank at least half-full)
- If the sprayer is equipped with multi-nozzle bodies with two or more nozzle sets, the lateral distribution (VK < 10 %) of all nozzle sets must be checked
5 Literature
- DLG Expert Knowledge Series 452 Lagerung von Pflanzenschutzmitteln auf dem landwirtschaftlichen Betrieb (Storage of crop protection agents on farms)
- DLG Expert Knowledge Series 409 Correct crop protection – things to check before you start
- DLG Expert Knowledge Series 413 Pflanzenschutz ohne Wasser zu gefährden (Crop protection without endangering water)
- DLG Expert Knowledge Series 467 Crop protection sprayer technology
- Technical Monograph No. 2, CropLife International, www.croplife.org
- German Crop Protection Act (Plant Protection Act – PflSchG), from 06.02.2012
- Personal protective equipment when handling crop protection agents, BVL 2020, www.bvl.bund.de/psa
Authors
- Harald Kramer, Landwirtschaftskammer Nordrhein-Westfalen, Münster
- Prof. Dr. Sven Reimann, Hochschule für Technik und Wirtschaft Dresden
- Dr. Norbert Uppenkamp, formerly Landwirtschaftskammer Nordrhein-Westfalen, Münster
with the involvement of the DLG Committee for Technology in Crop Production